Article
Design for Automated Manufacturing in Mechanical Engineering
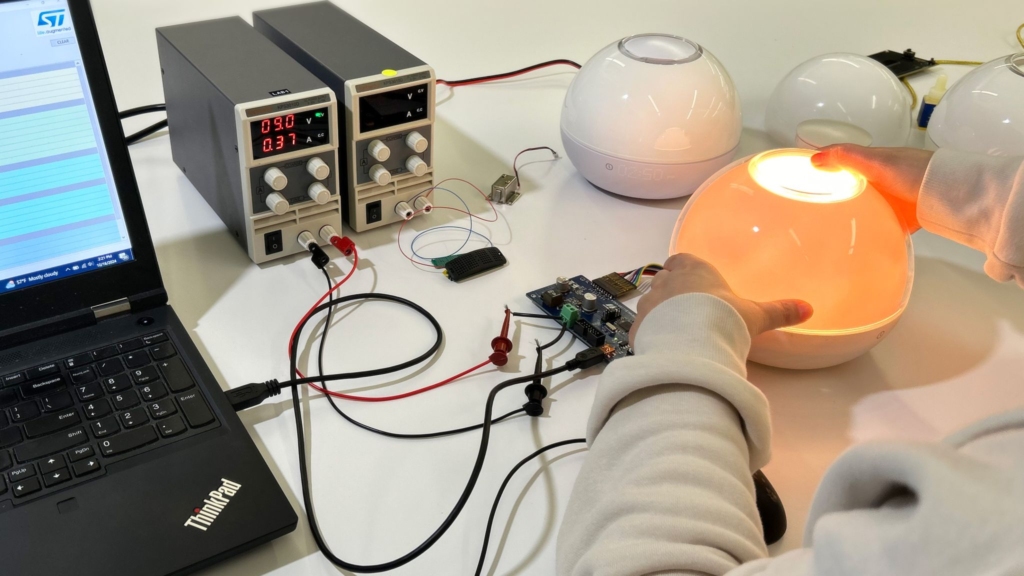
Understanding design for automated manufacturing
Design for automated manufacturing focuses on optimizing product design to enable efficient, accurate, and cost-effective production using automated manufacturing processes. Mechanical engineering specialists and electrical engineering specialists need to influence Industrial Design concepts and plan how Industrial Design concepts will be manufactured well before detailed design begins. Design tradeoffs need to be evaluated between how the parts will be manufactured and how the part will be assembled, inspected, and packaged via automation.
If design for automated manufacturing is not addressed early on in the design process it will often lead to the following manufacturing issues:
- High operational costs
- High assembly cost
- Low yield
- Poor product quality
- High parts cost

What are the benefits of design for automated manufacturing?
- Reduced operational costs: Automation has the potential to significantly decrease operational costs by reducing manual labor and minimizing waste, allowing companies to allocate resources to higher-value tasks
- Improved product quality: Design for manufacturing has the potential to enhance product quality through consistent and accurate manufacturing processes, reducing defects and ensuring higher customer satisfaction
- Higher Return on Investment (ROI): By reducing material costs, build times, and post-processing expenses, design for automated manufacturing maximizes the value of automated manufacturing investments
- Accelerated time to market: By streamlining design and production processes, design for manufacturing helps manufacturers bring products to market faster, giving them a significant competitive advantage
- Avoidance of assembly issues: Automated systems minimize human error, ensuring consistent quality control throughout the production process
- Enhanced sustainability in manufacturing: Automated manufacturing reduces material waste and energy consumption, leading to a smaller environmental footprint and cost savings
- Lower parts and assembly costs: One of the key benefits of designing for automated manufacturing is reducing the number of parts in a product, thus simplifying assembly processes and lowering overall production costs while maintaining quality
- Improved repeatability, consistency, and production efficiency: Designing for automation—and leveraging automated manufacturing processes—enables higher production volumes with fewer errors, improving overall efficiency and enabling scalability
- Easier inspection and testing processes: Design for automated manufacturing focuses in part on simplified prototyping and validation, optimizing designs early in the process to mitigate production challenges before they arise
- Enabling local manufacturing vs. overseas production: Design for manufacturing can better facilitate local production by making it cost-effective, reducing reliance on overseas manufacturing and the associated logistical challenges of such workflows
Tips for Designing for Automated Manufacturing
- Start during the pre-design stage
- KISS – Keep it simple
- Standardise – use the same part wherever possible
- Reduce parts where possible
- Design parts so they are easy to handle, singulate, and symmetrical
- Avoid Fasteners where possible
- Avoid flexible cables where possible. Difficult process to automate.
- Incorporate Self-Aligning Features – Tabs, Slots, Chamfers
- Have a base part that can be easily fixtures and facilitate a layered assembly
Design for automated manufacturing across industries
Consumer Product Design
Designing for automation is often required to produce a competitive product. Products where design for automated manufacturing is utilized properly will reduce waste, reduce material cost, and increase product yield and quality. Additional upsides include higher customer satisfaction because the product will be more dependable and reliable. This leads to higher product ratings and sales. Example: Samsung Galaxy’s – Automated Manufacturing and Testing
Industrial Product Design
Industrial products are often required to perform safety functions that industry relies upon. These products include circuit breakers, GFCI devices, variable frequency drives, motors, and safety switches. These products involve complex components that are difficult to manufacture using traditional methods, leading to multiple parts and assembly issues. Designing for automated manufacturing ensures that product performance is consistent, predictable, and reliable. Example: MCB Miniature Circuit Breaker Automatic Assembly Line Automation Equipment Plant Automation
Agricultural Product Design
Agricultural equipment needs to be dependable, reasonably priced, and easy to service. In addition, equipment is large and that often influences the desire to produce this equipment in high labor cost areas such as the United States. For this reason, design for automated manufacturing is a critical process in the agricultural industry. Agricultural companies such as John Deere invest up front to ensure product reliability and reduce waste. Example – John Deere utilizing AI to inspect for weld defects to ensure their product is more reliable and reduce product waste.
Aerospace
Aerospace products must meet stringent safety and material property standards. To be competitive, aerospace manufacturers employ complex manufacturing processes including carbon fiber reinforced polymer (CFRP) to produce large aerospace structures. Large CFRP structures present special challenges in the design, manufacturing, and inspection. The material is not homogenous and the orientation of the sheets must be positioned accurately for the structure to meet the designed strength. Furthermore, the structures are large and require tight tolerances. Example: Highly automated manufacturing process for large aircraft structures in dry CFRP design
Medical Device Manufacturing
Medical device manufacturers face stringent regulatory requirements, including the need for thorough testing and validation of the manufacturing process. For example, Insulet produces the Omnipod product in a clean room and each Omnipod is subject to over 100 automated quality inspections. Ensuring the quality and consistency of medical devices is crucial. Issues such as non-conforming materials, component failures, and the risk of product recalls can have severe consequences, including financial losses and damage to reputation. Design for automated manufacturing ensures the product is designed for automated assembly and inspection simultaneously. This ensures quality and compliance. Example: Insulet Acton Facility
Key considerations when designing for automation
#1: Design for High Volume Manufacturing
The higher the volume, the higher the incentive to invest in automated manufacturing. High-volume manufacturing processes require higher upfront tooling costs but deliver lower part costs. Typical high-volume manufacturing processes include injection molding, extrusion molding, stamping, and die casting. All of these processes come with limitations that need to be taken into account early in the design process.
#2: Pre-Production Design and Validation
It is essential to iterate on prototypes multiple times to fine-tune the design. During the early pre-design phase product requirements are solidified which leads to a formalized test plan which is used to validate the product meets the requirements. Prototyping and testing multiple cycles until the product meets these requirements is necessary. Design for manufacturing is employed during this process to fine-tune part geometries to optimize part geometry for automated manufacturing while also ensuring the product meets design requirements.
#3: Electronics Housing Design
The electronics housing protects the electronics from damage. Design for automated manufacturing must be utilized so that the electronics housing can meet product requirements economically and reliably. Typical features of electronics housing that facilitates design for manufacturing:
- The base part in which the assembly will be built.
- Built-in layers in as few parts as possible.
- Automated sealing in between layers.
- Ability to release heat from the enclosure
- Chamfer/ Radiuses and aligning feature to allow compliance during assembly
- Snaps preferred over screws in the assembly process
#4: Tolerance Analysis and GD&T
Tolerance analysis is critical to the design of an economical product. The tighter the tolerance the more expensive the tooling costs will be. If the tolerances are specified as too loose the yield and assembly will suffer. For high-volume manufacturing, a detailed statistical analysis is required to confirm a high probability of parts fitting together during the assembly process.
#5: FMEA (Failure Mode and Effects Analysis)
FMEA is a systematic, step-by-step approach to identify and prioritize possible failures during the design and manufacturing process. DFMA should be included in the scope of FMEA studies to reduce problems in that automated manufacturing process. FMEA should be performed at all phases of the product development process in order to identify and mitigate issues as early as possible. For more information on FMEA please refer to this link.
#6: Injection Molding and Plastic Part Design
Injection molding is the most popular process for high-volume manufacturing. Common design considerations include cosmetic and mating features. The designer of the parts wants to maintain near-uniform wall thickness to avoid shrink with draft angles that allow the part to be easily separated from the mold. Employing design for automated manufacturing principles, the engineer needs to envision the tooling that creates the part while designing the parts. To minimize the number of parts the engineer may choose to utilize more expensive and complicated tooling.
#7: Fixture Design
Fixtures are required throughout the automated manufacturing process. Although design of the fixtures themselves is typically performed by the automation team, the parts need to be designed so that they can be fixtured. A big part of designing for automation is considering how product parts will be fixtured during the product development process. Fixtures are required for automated assembly, inspection, testing, and packaging. If the parts aren’t designed keeping fixturing in mind – automated manufacturing won’t be an option.
#8: Design for Ingress Protection
The required IP rating is determined early in the Product Development process and needs to be included in the product testing. The first digit represents ingress protection with respect to dust and the second digit represents ingress protection with respect to liquid. Ingress protection for products are specified by IEC 60529. For more information on specifics see this link.
In order for products created by automated manufacturing to meet specific ingress protection requirements automated sealing methods are often required. These sealing methods often include:
- Form-in-Place-Foam-Gasket (FIPFG)
- Ultrasonic Welding (Plastic)
- Laser Welding (Plastic)
- Automated O-ring placement
- Automated Adhesive/Sealant Dispensing
Looking for design for automated manufacturing solutions and related engineering services? Let’s connect.
Design for automated manufacturing is essential to the success of the product development process. Designing for automation reduces waste, improves product quality, and reduces product cost. Future trends in design for automated manufacturing will be heavily influenced by advancements in AI, robotics, IoT, and sustainability practices. These developments will make automated manufacturing systems more adaptive, efficient, and capable of handling increasingly complex designs.
Design for automated manufacturing is a must for effective and competent product development. Fresh Consulting is a multi-disciplinary design firm capable of guiding your product through all phases of the design process from strategy to mass manufacturing. Let us know if you need help turning your big idea into a real product.